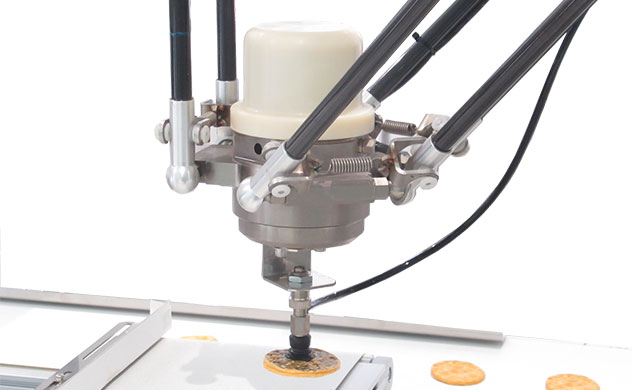
In the food industry, where labor shortages are becoming more serious while stable quality is required, we are actively promoting initiatives to reduce the number of employees in the quality inspection process. For example, at the production site of foods with various individual differences, e.g. bread and sweets, the standard inspection such as scorching, uneven baking, cracking or chipping. Many of these inspections are done manually, making it difficult to quantify the criteria for good or bad products.
This system employs an image determination service called Y’s-Eye, which uses deep learning AI technology to automatically determine complex No-Good patterns with the same level of accuracy as humans. Because the interface does not require expert knowledge of AI or image processing, the introduction difficulty is lowered. If additional learning is repeated, detection accuracy can be further improved, and inspection efficiency and quality can be stabilized. As a manufacturer of industrial robots, Yaskawa offers total solutions, including options for robots to eliminate defective products.
Further demands in the food industry include various inspection processes, such as contamination inspection, toppings leakage inspection, and packaging and appearance inspection. In addition to food products, we have achieved results in a number of industries, including quality inspection of industrial parts such as metals, and detection inspection of contamination during plastic molding.
Yaskawa’s solution concept, i3-Mechatronics, goes beyond automating factory facilities through digital data management. We will ensure stable production quality by automating the “inspection process” using AI, which must rely on the skills and experience of expert workers, and by accumulating digital data from “manufactured products.”.
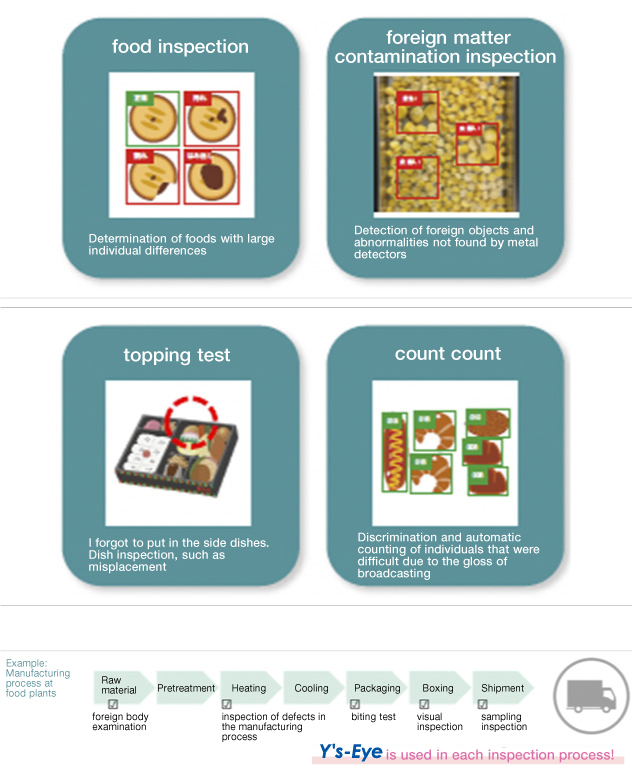