1) Composition of Industrial Robots
Industrial robots consist mainly of the following four components.
- The “manipulator” that corresponds to the robotic arm
- “Robotic controller” controlling the manipulator
- “Programming Pendant” for monitoring operation
- “Power supply cable” connecting the manipulator to the robot controller
In order to perform the actual work, a robotic hand attached to the manipulator, a tool such as a welding torch (end effector), a jig for fixing the workpiece, and a sensor for detecting the workpiece are combined.
2-1)What are manipulators?
Manipulators are the equivalent of moving and working arms, and when you hear about industrial robots, this is what you first imagine. Manipulators typically have four to seven rotating shafts, each of which is connected to a servo motor and a speed reducer. The six moveable parts (called six degrees of freedom) manipulators, which are the most produced in Yaskawa, can operate in position (x, y, z) and posture (θx, θy, θz) in three-dimensional space. For palletizing robots that do not require six degrees of freedom, there are also four-axis robots, and for robots that require more degrees of freedom, there are seven-axis robots.
2-2)Manipulator type
2-2-1) Vertical articulated type
6-axis vertical articulated robot
At present, the mainstream of industrial robots is 6-axis vertical articulated robots. When you hear the word “robot,” I think you first imagine it. This versatile robot can be used for various purposes when considering automation. Even with the same 6-axis robotic structure, there are various types with the maximum weight that can lift the object ranging from 500 g to 900 kg. The 500 g transportable model weighs only 7 kg and can be carried with one hand. If you combine several of them, they work together to perform detailed work precisely. Industrial robots can perform various robotic tasks with tools from the wrist to the tip.
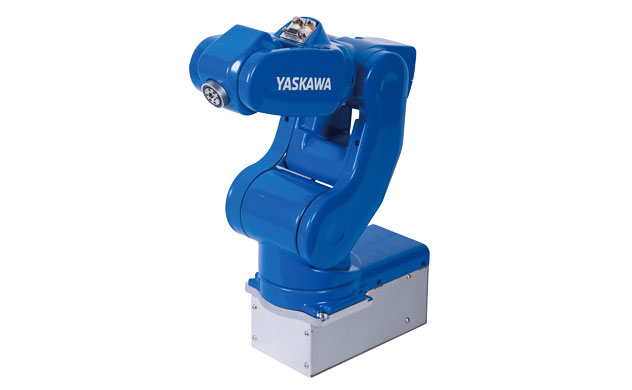
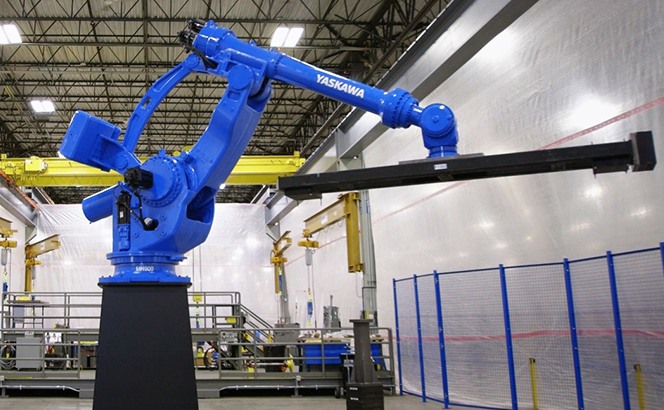
7-Axis vertical articulated robot
It is said that if there are 7 axes, it can move closest to a human arm. Even when approaching a place where the manipulator cannot reach with 6 axes, the robotic arm can come around and approach with another axis, so the equipment can be arranged in smaller and higher density, and the flexibility of the line layout of the factory is increased. In 2008, we commercialized the world’s first 7-axis arc welding robot.
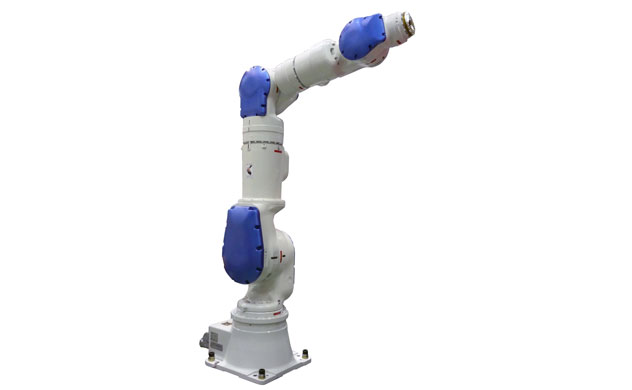
Dual arm type robot
The shape of a dual-arm robot looks like a human upper body, and the number of axes is 15 with 7 axes of both arms, which are similar to the actual movement of a human arm and of additional one axis of swinging the hip, making it possible to move almost like a human. In other words, industrial robots can learn to replace the work that humans have done in factories. In the case of cardboard packaging, one arm holds down the work piece and the other arm packs, which is similar to human movement. Yaskawa’s ice cream robot character “Yaskawa kun” will automatically make ice cream using the two robotic arms.
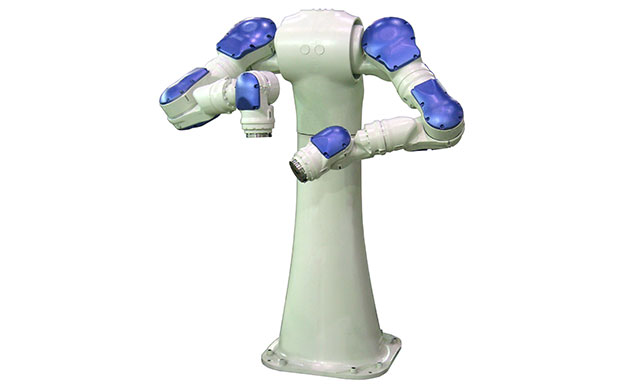
Collaborative robot
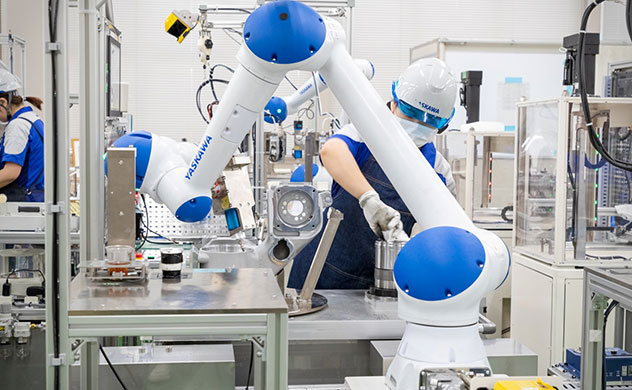
2-2-2) Horizontal articulated type (SCARA robot)
The “SCARA” robot stands for Selective Compliance Assembly Robot Arm. The number of axes is generally 4, and the movement is a combination of the robotic arm turning horizontally and the tip moving vertically. Because of its simple robotic structure, it can operate at high speed, and because the tip part moves up and down, it is good at mounting electronic components on printed circuit boards.
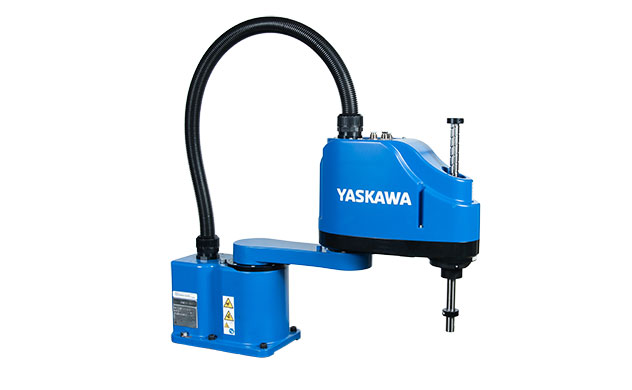
2-2-3) Parallel link
It has a robotic structure in which 3 arms extending from the body are connected at the tip. The tool is attached to the tip. The robotic arm itself can be made very lightweight, so it can move at high speed. The motion range is small, but because each motor synchronizes to operate the tip, very fast “speed” is obtained with respect to the carrying capacity. It is widely used in food factories and food processing plants, and it arranges, fills, closes, packages, and packs products that flow through production lines.
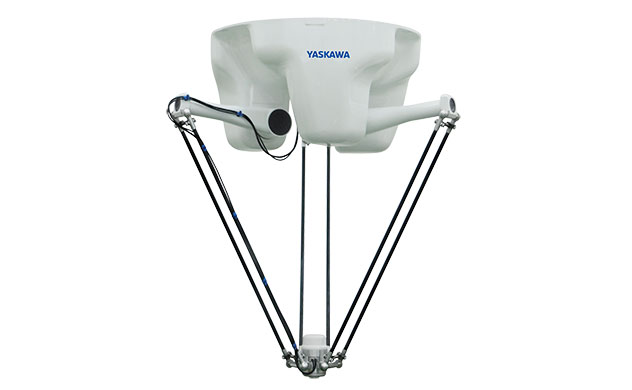
2-3)Components of the manipulator
Servo motor
It moves the manipulator by the command from the robot controller. The servo motor is equipped with an encoder to detect the speed and rotational position, which is fed back to the robot controller to achieve highly accurate operation. If the manipulators are 6 or 7 axes, it is equal to the number of servo motors installed.
Speed reducer
It slows down the rotational speed of the robotic arm and increasing the torque are transmitted to the manipulator. The torque output via the reducer is proportional to the reduction ratio. Speed reducer used in industrial robots generally have a robotic structure in which the input shaft from the servo motor and the output shaft after reduction are collinear. The accuracy of the speed reducer is an important component that affects the accuracy of the manipulator operation.
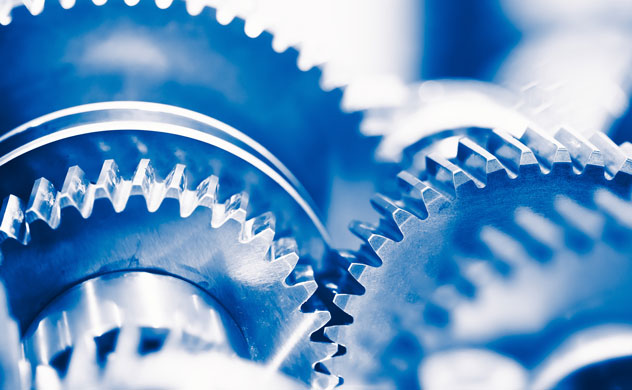
3)Robotic controller
A robotic controller is a part of the brain that contains a CPU for recording a program to operate an industrial robot and calculating a command value to operate it concretely, an I/O board for controlling input/output signals, and a servo driver for operating a manipulator and supplying power. In recent years, there have been many requests for down sizing to save space issue for installation on site and Yaskawa developed the YRC series, which is one of the world’s smallest robotic controller.
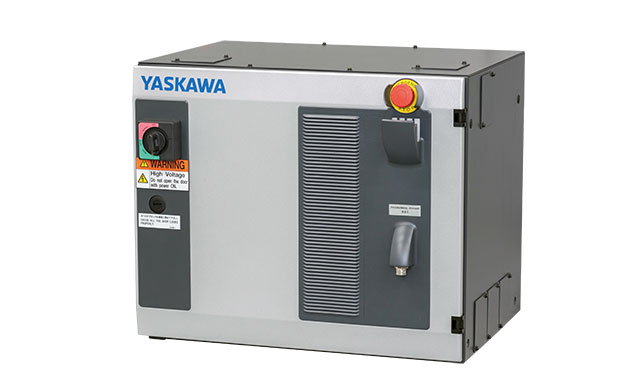
4)Programming pendant
A programming pendant is a human-machine interface that teaches manipulators how to work, sets programs and conditions, and checks the operating status. The programming pendant is equipped with what is called a dead man switch, and the industrial robot is not supplied with power unless the operator holds the programming pendant properly.
It is also designed with safety aspect that the power supply to the industrial robot is cut off even if the operator holds the programming pendant tightly in some dangerous condition.
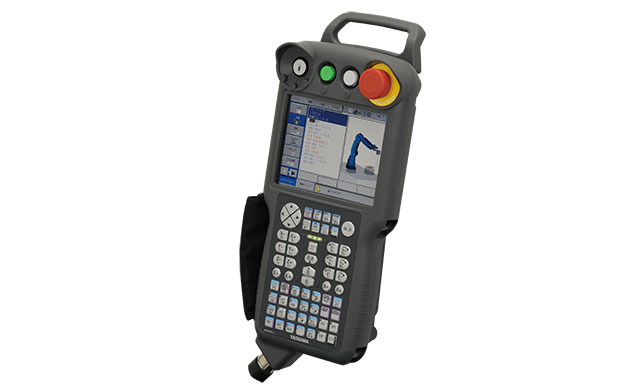
5)Tools (End effector)
The robotic hand, welding torch, and spot gun attached to the wrist of industrial robots are collectively called tools or end effectors. Tools /end effectors may be prepared in advance by peripheral manufacturers, or they may be designed and built specifically for each work.
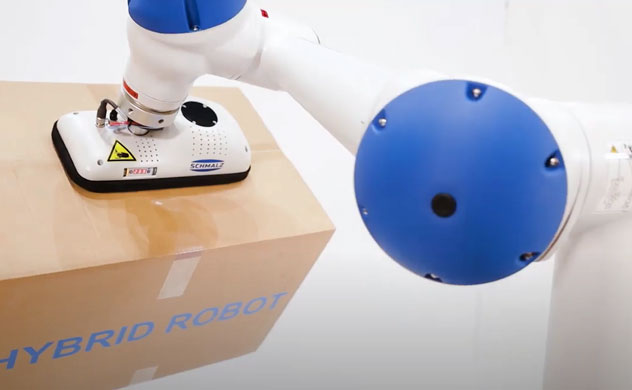