-
Both servo motors and stepping motors are synchronous motors that can control position. In general, stepping motors are suitable for use cases of slow speed in short distance which does not require much accuracy in positioning.
On the other hand, servo motors contribute to use cases that require high positioning accuracy, long distance moves or need to generate high torque in high speed. Servo motors, however, would have lower follow-up toward commands if the rigidity of equipment is insufficient, while stepping motors always provide high follow-up performance regardless of the equipment.
Then, stepping motors are rather inexpensive because of their simple structure, while servo motors are relatively expensive since they require the encoder to detect position.
However, servo motors would contribute to significant energy saving thanks to the less calorific value they generate, which would lead to reduce running cost.
Difference in resolution depending on the rotating mechanisms
In the case of stepping motors, the motor has small teeth on it in order to operate positioning depending on the small teeth (step angle). The driver (amplifier) generates command signals toward the motor based on the timing of pulse train signal input in controller as a positioning command.The motor rotates at the designed step angles (resolution).
However, the resolution is limited as it requires high machining accuracy. In the case of servo motors, the motor mounts an encoder and has a mechanism to feedback rotating position and speed of the motor shaft to the driver (amplifier). The driver (amplifier) calculates the deviation of the commands on position/speed and the feedback signals (current position/speed) from encoder, and controls the rotation of the motor so as to keep the deviation “0.” Servo motors realize high resolution by this mechanism.
Difference in torque characteristics depending on control systems
Stepping motors do not have a position detection sensor such as an encoder, instead they control the operation between the driver (amplifier) and the motor with the open-loop system. Therefore, it could cause motor step-out when the allowable torque or more is applied to the shaft from the outside.
On the other hand, servo motors always have feedback of position information from the encoder between the driver (amplifier) and the motor, and control the operation with the closed-loop system. Therefore, they are able to correct a temporary positioning fluctuation due to the external force exceeding the allowance and check the status with such as the completion signals of positioning.
In addition, servo motors are able to generate the same level of torque both in low-speed region and in high-speed region. Although stepping motors generate high torque in low-speed region, it lowers torque when the speed gets higher.
Difference in electricity consumption and heat generation depending on the structures
Stepping motors keep the flow of electric current through motors at a certain level when they are either operating or stopped. And the loss would increase depending on motor’s rotating speed, so that it increases both electricity consumption and heat generation for that.
On the other hand, servo motors require electric current only corresponding to the deviation, it is able to lower electricity consumption and suppress motor’s heat generation as it needs small amount of electric current when the motor stops or is operating at a constant speed.
Comparison of heat generation and power consumption in case that positioning operation is repeated under the same conditions
-
Both AC drives and servos are equipment to control motors. Both have the same basic function that rotates motors at an expected speed by converting power from commercial power sources, controlling voltage (current) and frequency. Customers will choose either one of these depending on the performance and the function they need. AC drives have a perfect command of the motor’s rotation speed and supply stable power. And they are constantly advancing by implementing functions which were used to be controlled by host controller as the standard. In addition, 1000 Series AC drives realize controls on various types of motors. They are able to control not only general induction motors but also efficient synchronous motors (with/without PG). There is a wide range of usage for AC drives from living-related devices and social infrastructure facilities that are close to our daily lives to industrial equipment. Moreover, they also contribute to saving energy for the use of fans and pumps by adjusting motor’s rotation speed and suppressing the waste of the electricity consumption.
On the other hand, servos control motors so as to follow-up toward commands of position and speed quickly.The motor controls the dedicated synchronous motor which comes with the encoder. Servos demonstrate a great performance on moving surely and faithfully to the commands of position and speed, so that equipment such as machine tools and semiconductor manufacturing equipment, which requires high-speed and high-accuracy positioning, applies servos.
-
Machine controller and PLC (Programmable Logic Controller) are both controlling devices for machines. PLC has been generated for the purpose of replacing the electromagnetic relay, used in the conventional automation system and executes control based on the preset order. This is called “sequence control”.
Meanwhile, various machines have been required to offer a higher technical advantages in recent years. Then, a machine controller was generated to control various devices that perform complex motions at high speed using servo and AC Drives. In this background, machine controller and PLC have different purposes, so they are good at different jobs. Machine controllers are good at controlling complex motions at high speed and with high precision, whereas PLCs are good at input / output (I/O) control.
Learn more about Servo motors
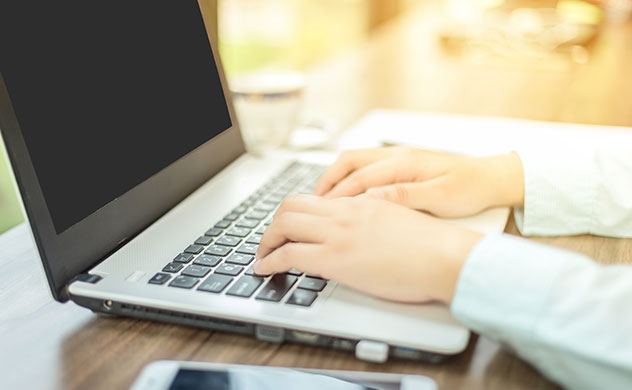
Introduction of Industries Supported by Servo motor
This section introduces servo motors that support our daily life.
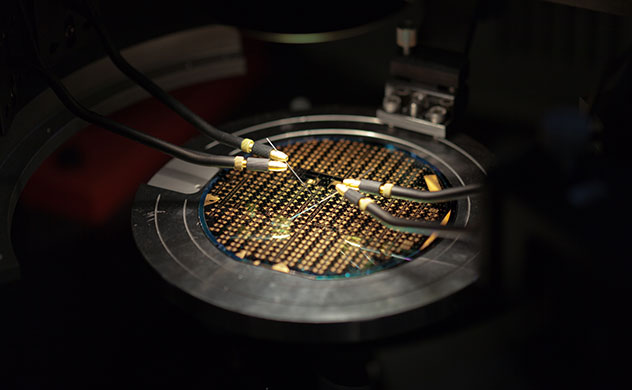
Application in which Servo motor Works
This section introduces servo motors that support the industries around you.
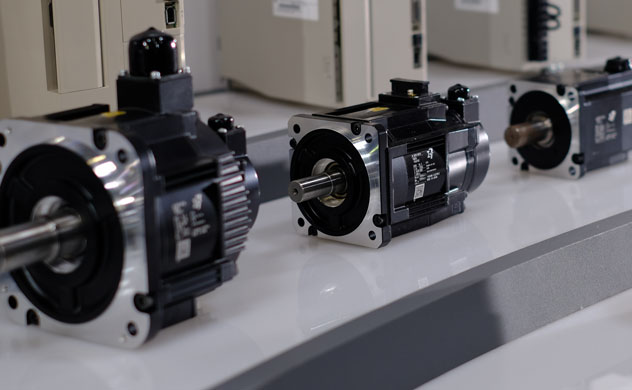
Servo motors With Various Types
At the request of our customers, we offer a wide range of motors, including rotary motors, linear motors/linear sliders, and linear motors, that meet the required force (torque) and mechanism.
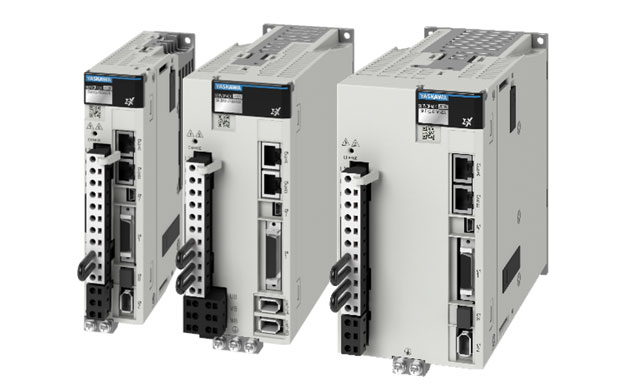
Products that Support Servo motors
This section introduces products that support the high performance of servo motors, such as sensors, amplifiers, and controllers.
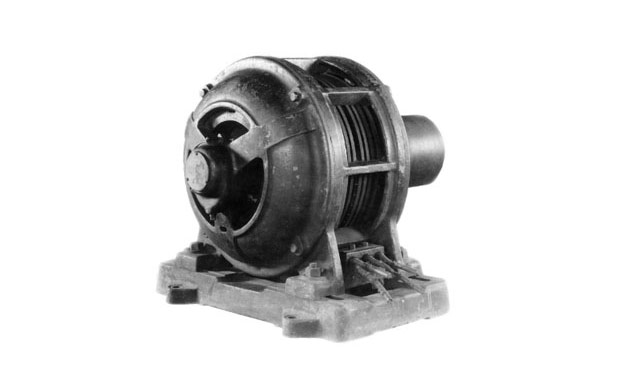
What is a Motor?
This section introduces the beginning of motors, practical applications, and types of motors.
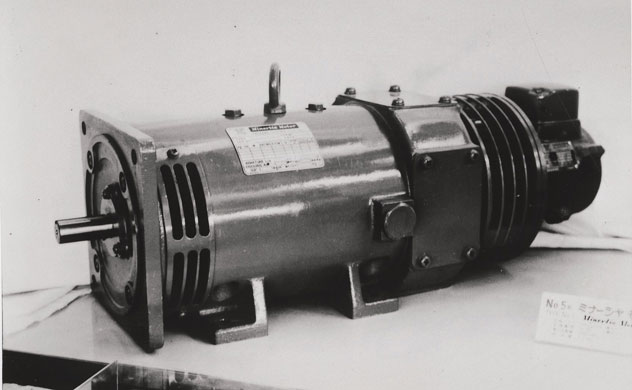
History of Servo motors
This section introduces the history of the development over the past 50 years, starting from the legendary Minertia Motor in 1958
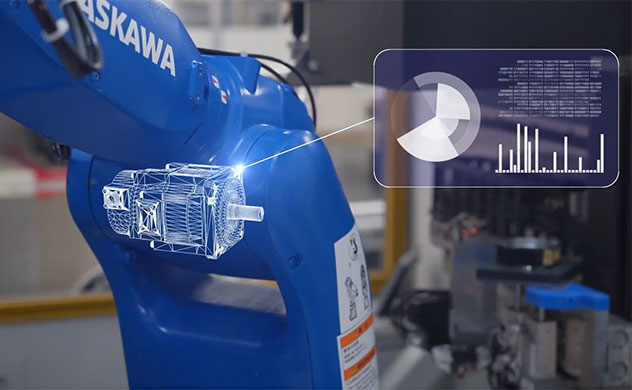
Future of Servo motors with Response to IoT
Servo motors themselves act as sensors in our customers’ efforts to build smart factories, and they become key components that enable us to monitor the operating status of Yaskawa products.